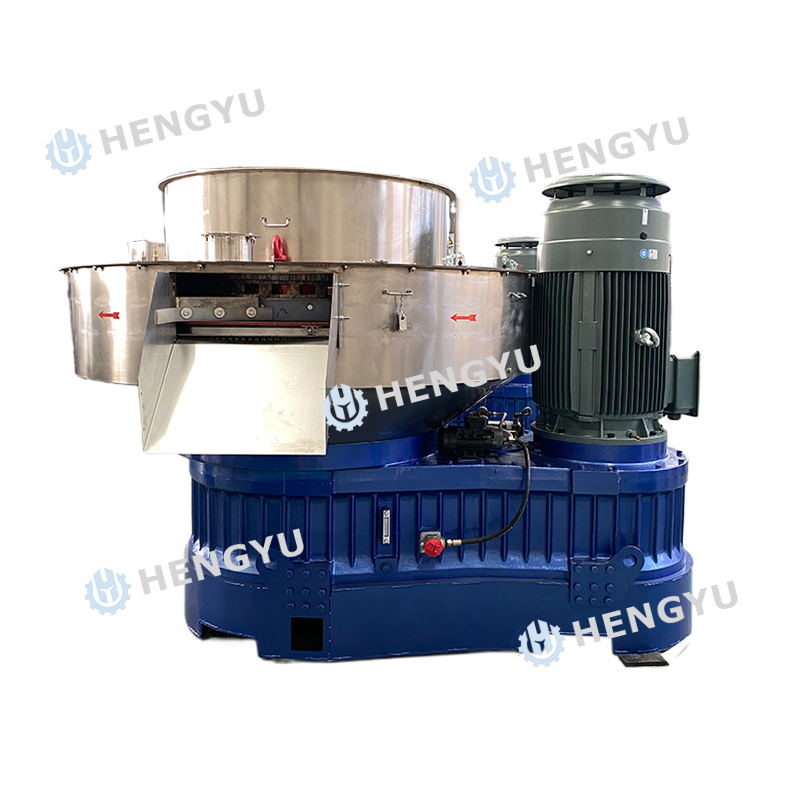
RDF Solid Waste Briquetter
Keywords:
RDF Solid Waste Briquetter
Products
About Us
Enterprise strength
Product Overview

Describe:
RDF Solid Waste Briquetting Machine is mainly used to process all kinds of solid wastes, such as shoe and clothing trimmings, leather, paper mill paper residue, domestic garbage, stale garbage, sludge and so on. Through a series of processing, these wastes are compressed into block fuels with certain shapes and densities for transportation, storage and further utilization. This kind of equipment usually consists of several parts, such as feeding system, compression system, molding system, power system and control system, etc. All parts work together to realize efficient processing and transformation of solid waste.
RDF solid waste briquetting machine is widely used. In the electric power industry, it can help coal-fired, thermal and thermal power plants to realize green and low-carbon transformation; in the field of garbage incineration, it can make RDF fuel rods from garbage to be used in incineration power plants, which can improve the calorific value and reduce the cost; and in the field of industrial kilns, such as cement plants, it can be used to replace coal with RDF fuel, so that it can reach the goal of “turning waste into treasure”.
Specificity:
01Strong adaptability: it can process many types of solid waste, including those with different compositions and humidity, and can adapt to complex waste sources and compositions.
02High efficiency and energy saving: Adopting advanced compression technology and power system, it can realize high production efficiency and reduce energy consumption under the premise of guaranteeing the quality of briquettes. For example, some RDF solid waste briquetting machines reduce energy loss and improve energy utilization by optimizing the design of the hydraulic system.
03Good environmental performance: In the process of processing, it can effectively reduce the pollution of waste to the environment. On the one hand, through compression and molding, it reduces the volume of waste and reduces the occupied space in landfills; on the other hand, the RDF fuel made produces relatively few pollutants during combustion and has a high combustion efficiency, which helps to reduce greenhouse gas emissions.
04High degree of automation: Equipped with advanced control system, it can realize automatic operation and reduce manual intervention. The whole process from feeding, compression to molding can be precisely controlled by preset programs, which not only improves production efficiency and product quality stability, but also reduces manual labor intensity and operational risks.
05High product quality: The RDF briquettes produced have high density and strength, which is convenient for long-term storage and long-distance transportation. Meanwhile, due to the screening and treatment of waste materials in the process, the calorific value of RDF fuel is improved and the combustion performance is more stable, which can meet the combustion needs of different industrial fields.
Product Details

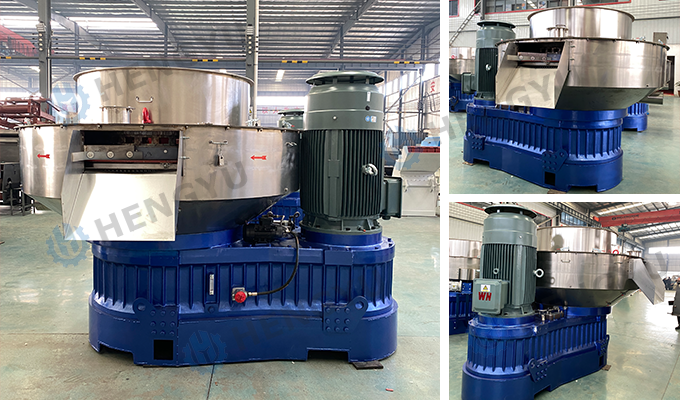
Working Principle
Feeding stage: Solid waste is transported to the compression chamber of the briquetting machine through the feeding device. The feeding device usually consists of a conveyor belt, a hopper and other components, which can evenly feed the waste into the machine and ensure the stability and continuity of the feeding.
Compression stage: The waste entering the compression chamber is compressed under strong pressure. The briquetting machine generally adopts hydraulic system or mechanical transmission system to provide pressure, through the press head, piston and other parts of the waste extrusion, so that its volume is gradually reduced, the density is increasing. In this process, the air and moisture in the waste are partially extruded to prepare for the subsequent molding.
Molding stage: The compressed waste is pressed into specific shapes, such as blocks, columns, etc., under the action of the mold. The shape and size of the molds are designed according to the actual needs. The molded RDF fuel has a regular shape, which is easy to handle and store, and also helps to improve the combustion efficiency.
Main Technical Parameters

Model No. | Number of molding holes (pcs) |
Power (kW) |
Capacity (t/h) | Overall dimensions (mm) |
9JK-2600 |
52 |
75 |
1-2T/H |
2647×2100×1900mm |
9JK-3500 |
72 |
110 |
2-3T/H |
3250×2600×2000mm |
9JK-4500 |
88 |
132 |
3-4T/H |
3350×2800×2200mm |
9JK-5500 |
100 |
160 |
3.5-4.5T/H |
3000×2300×2000mm |
Model 9JK-5500 All-in-One 100, 101 holes, 102 holes can be customized |
100/101/102 |
160 |
4-5T/H |
3000×2400×2000mm |
9JK-6500 |
120 |
200 |
4-5T/H |
4400×2970×2495mm |
9JK-7500 |
136 |
250 |
5-6T/H |
4400×2970×2495mm |
9JK-8500 |
176 |
250 |
6-8T/H |
3000×2400×2000mm |
Work Scenario

Biomass curing fuel can be widely used in bio-stoves, heating stoves, hot water boilers, steam boilers, drying stoves, biomass gasification stoves, and biomass power plants.
It mainly includes: feeding system, moulding system, discharging system, heating system, distribution cabinet control system and so on.
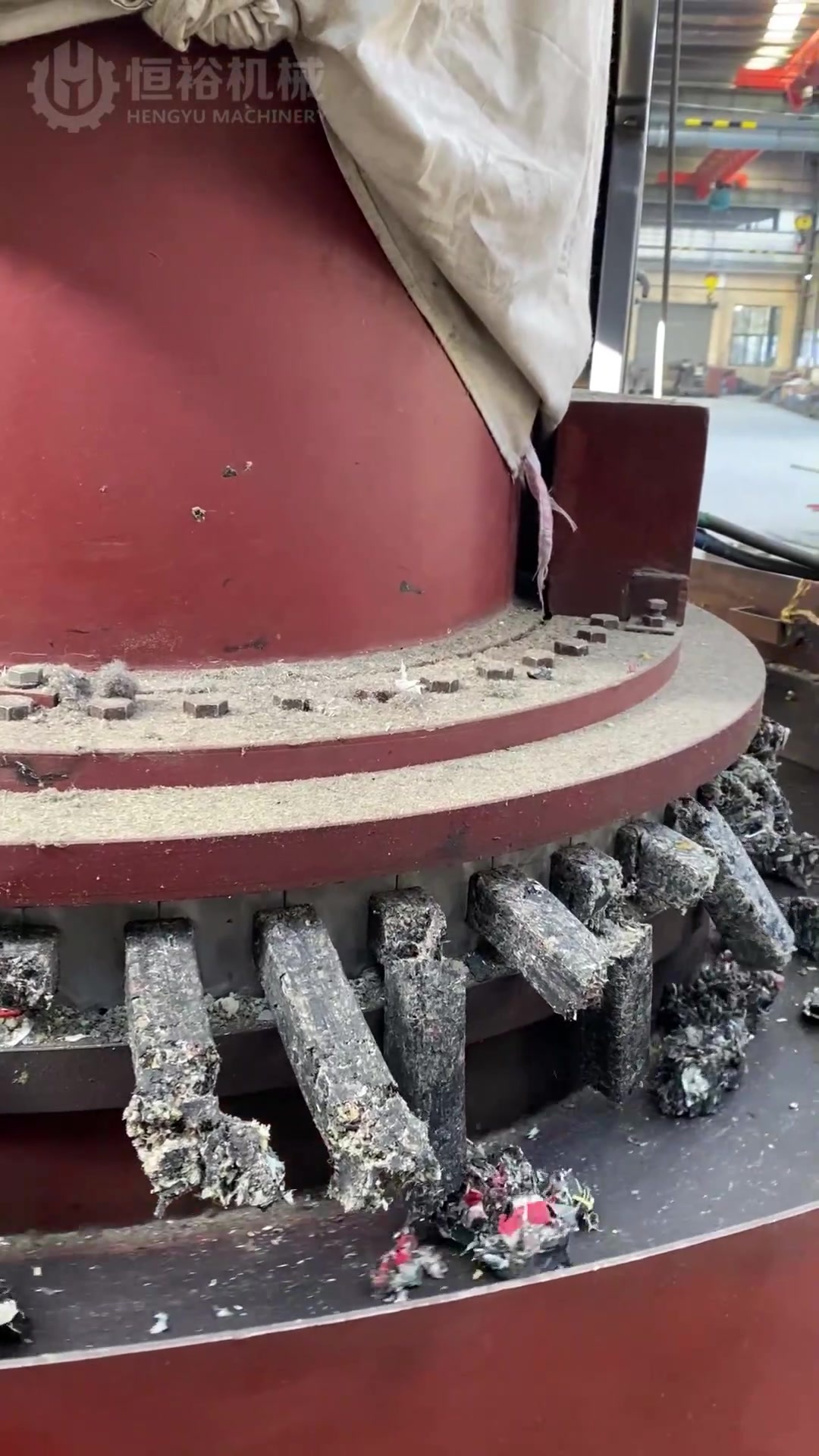
RDF Solid Waste Briquetter 02
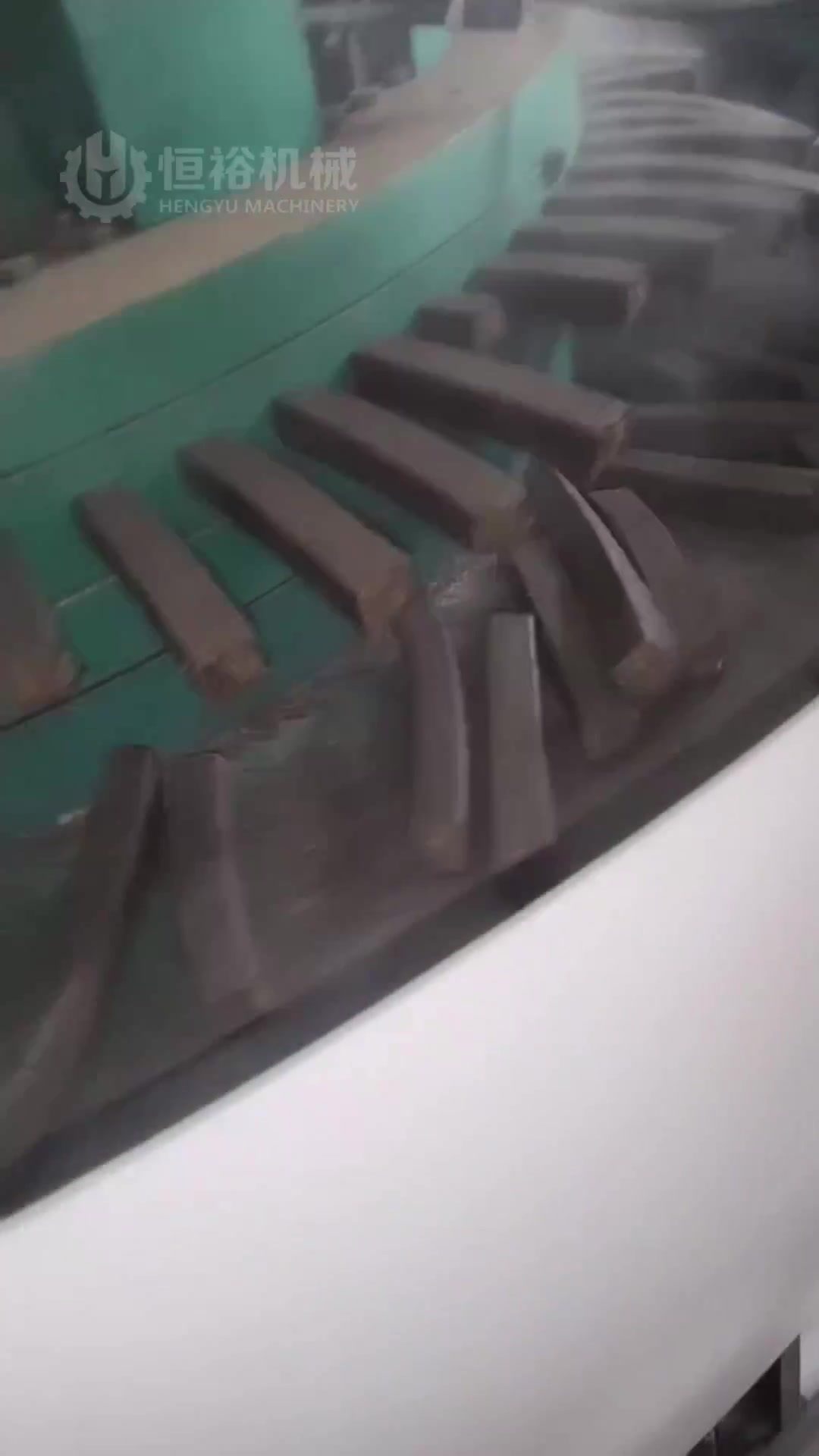
RDF Solid Waste Briquetter 01
Send Inquiry
Leave a message immediately and receive free product consultation. We will arrange experts to contact you as soon as possible.